Die Konversion langkettiger Kohlenwasserstoffe in kurzkettige Kohlenwasserstoffe, die bei der chemischen Verarbeitung von Erdöl entstehen, erfolgt durch den chemischen Prozess Cracken.
Dabei unterscheidet man in die zwei Hauptformen katalytisches und thermisches Cracken.
Grundlagen Cracken
Der Begriff Cracken stammt aus dem Englischen und bedeutet so viel wie “brechen” oder “spalten”. Dieses Verfahren eignet sich zur Verarbeitung von Erdöl und folgt auf die Destillation des Rohöls. Das Ziel ist, mithilfe des Cracken Benzine zu gewinnen. Bei der Rohöldestillation entstehen nur circa 20 % Benzine und etwa 30 % andere Produkte mit einem Siedebereich unter 360 °C. Die größte Menge bilden die sogenannten hoch siedenden Schweröle.
Schweröle sind langkettige Kohlenwasserstoffe. Sie bleiben als sogenannter Rückstand bei der fraktionierten Destillation von Erdöl zurück. Sie bilden den nicht verdampfbaren Teil eines erdölverarbeitenden Prozesses, den Sumpf. Da die Nachfrage an kurzkettigen Kohlenwasserstoffverbindungen wie Benzin oder Dieselöl jedoch größer ist, werden die langkettigen Moleküle umgewandelt.
Vorgang des Crackens
Um die langkettigen Kohlenwasserstoffe () zu trennen, werden diese auf eine Temperatur von über 400 °C erhitzt, sodass sich die C-C Bindungen in einer endothermen Reaktion spalten. Es entstehen kurzkettige Moleküle. Die Konversion der Rückstände kann auf unterschiedliche Arten erfolgen:
- thermisch ohne Katalysator
- unter Zusatz von Wasserstoff, das sogenannte Hydrocracken
- mittels anderer Katalysatoren, etwa der FCC-Prozess
Alle Formen des Crackens haben das Ziel, hochwertige Produkte wie Benzin zu gewinnen, um den nachgefragten Bedarf zu decken.
Formen des Crackverfahrens
Die Hauptformen des Crackverfahrens sind thermisches und katalytisches Cracken.
Thermisches Cracken
Entwickelt wurde das Verfahren des thermischen Crackens vom russischen Ingenieur Wladimir Schuchow 1891. Er war der Erste mit einer industriellen Anlage, die das thermische Cracken von Erdöl ermöglichte. Beim thermischen Cracken werden die entstandenen Kohlenwasserstofffraktionen in einem Druckbehälter stark erhitzt. Die Temperaturen liegen dabei zwischen etwa 450 °C und 800 °C.
Durch Erhöhung von Druck und Temperatur entstehen Schwingungen der langen Kohlenwasserstoffmoleküle, sodass diese Ketten in kleinere Ketten brechen. Die kurzkettigen Kohlenwasserstoffmoleküle werden als olefinisch bezeichnet. Auch eine Rekombination zu höher molekularen paraffinischen Molekülketten ist möglich. Dazu zählen etwa die Aromaten. Ein unerwünschtes Nebenprodukt ist der Kohlenstoff (Koks).
Das thermische Cracken unterteilt sich in vier verschiedene Verfahren, die der Herstellung unterschiedlicher Produkte dienen. Zu den Verfahren zählen:
- Steamcracking
- Visbreaking
- Delayed Coking
- Flexicoking
Katalytisches Cracken
Beim sogenannten katalytischen Cracken handelt es sich um ein Verfahren zur Aufspaltung langkettiger Kohlenwasserstoffe durch den Einsatz eines Katalysators. Die durch das Cracken entstehenden kurzkettigen Moleküle sind sehr reaktiv und können sich spontan umwandeln oder sich mit anderen Molekülketten rekombinieren. Dieses Verfahren dient der Gewinnung hochwertiger Benzine.
Fluid Catalytic Cracking (FCC)
Beim Fluid Catalytic Cracking, kurz FCC, handelt es sich um ein Crackverfahren mit einem bewegten Katalysator und ist der wichtigste Crackprozess.
Abbildung 1: Katalytisches Cracken
Der Ablauf des FCC-Prozesses lässt sich in vier Abschnitte unterteilen:
- Röhrenofen
- Reaktor
- Regenerator
- Fraktionierkolonne
Das bei der fraktionierten Rohöldestillation entstandene Vakuumdestillat, also die Schweröle, werden im Röhrenofen bei einer Temperatur von etwa 500 bis 600 °C verdampft. Die Produkte aus dem Verdampfungsprozess werden unter Zuführung eines reaktiven Katalysators in den Reaktor weitergeleitet.
Im Reaktor erfolgt die Spaltung, also das Cracken, größerer Moleküle in ein Gemisch aus kleineren Molekülen wie Gase, Benzin oder Petroleum unter Einfluss des aufgewirbelten Katalysators. Bei der Spaltung der Moleküle entsteht eine geringe Menge Koks, der sich am Katalysator ablagert. Diese Menge reicht bereits aus, um den Katalysator innerhalb weniger Minuten unwirksam zu machen.
Der dritte Schritt beschreibt die Regeneration des deaktivierten Katalysators im Regenerator. Dazu wird der deaktivierte Katalysator aus dem Reaktor in den Regenerator abgeleitet. Durch das Zuführen von Luft verbrennt das Koks und der Katalysator wird reaktiviert. Anschließend kann der reaktive Katalysator erneut zu den Produkten der Verdampfung hinzugefügt werden, um den Crackprozess zu wiederholen.
Die destillative Trennung der entstandenen Produkte bildet den vierten und letzten Schritt im FCC-Prozess. Dazu werden die Crackprodukte aus dem Reaktor in die Fraktionierkolonne eingeleitet, wo sich diese in die verschiedenen Siedefraktionen unterteilen. Dazu zählen:
- Crackgase
- Benzine
- Dieselöl
- Gasöl
- Rückstand
Hydrocracken
Das Hydrocracken ist ein Vorgang beim Cracken mit Zusatz von Wasserstoff – und damit Teil der Petrochemie. Dabei werden spezielle Katalysatoren eingesetzt. Durch das Hydrocracken sollen Zwischenprodukte gebildet werden, die zur Herstellung von begehrten Motorenbenzin, Kerosin und Dieselkraftstoffen dienen. Der Crackprozess wird bei einem Wasserstoffdruck bis 200 bar und einer Temperatur von über 400 °C durchgeführt.
Cracken – Das Reforming
Bei der Rohöldestillation entstehen zwar Benzine, jedoch mit einer schlechteren Qualität, da diese zum Klopfen neigen. Dieses Klopfen entsteht durch die verfrühte Entzündung des Luft-Benzin-Gemischs beim Verdichten des Motors.
Die Klopffestigkeit eines Kraftstoffes wird anhand einer Maßzahl beschrieben, die Oktanzahl (ROZ – Research Oktanzahl). Um die Klopffestigkeit zu erhöhen, können dem Benzin Antiklopfmittel zugeführt werden. Doch auch durch die Veränderung der Struktur kann die Klopffestigkeit erhöht werden.
Die Oktanzahl ist ein Maß für die Klopffestigkeit eines Ottokraftstoffes. Der Zahlenwert reicht dabei bis 100.
Einige Aromaten, Erdgas und Flüssiggas bilden Ausnahmen und können eine Oktanzahl größer als 100 aufweisen.
Beispiele für Okatanzahlen
Hier findest du eine Übersicht zu verschiedenen Oktanzahlen von Alkanen und Aromaten.
Oktanzahlen von Kohlenwasserstoffen | |||
n-Hexan: 25 | n-Octan: 0 | Cycloalkane: 70–90 | Benzen: 106 |
n-Heptan: 0 | iso-Octan: 100 | iso-Alkane: 70– >100 | Toulen: 115 |
Vorgang beim Reforming
Beim Reformieren von Kohlenwasserstoffen wird die Struktur umgewandelt, ohne die Größe des Moleküls zu beeinflussen.
Das Reforming ist ein katalytischer Prozess. Dabei werden Kohlenwasserstoffe mit einer geringen Klopffestigkeit (Oktanzahl) in Kohlenwasserstoffe mit höherer Klopffestigkeit umgewandelt.
Beim Reformieren laufen verschiedene Prozesse gleichzeitig oder nacheinander ab. Bei den Prozessen handelt es sich zum Beispiel um:
- Die Isomerisierung von n-Alkanen zu iso-Alkanen.
- Cyclisierung von kettenförmigen zu ringförmigen Alkanen.
- Dehydrierung von Cycloalkanen zu Aromaten.
Die Temperatur des Prozesses liegt zwischen 450 und 550 °C. Durchgeführt wird das Reformieren bei einem Druck von 1 MPa unter Zusatz von Wasserstoff an einem Katalysator aus Platin auf Aluminiumoxid. Das Aluminiumoxid dient als Katalysator bei der Isomerisierung und Cyclisierung der Kohlenwasserstoffe. Bei der Dehydrierung der Alkane dient das Platin als Katalysator.
Cracken - Das Wichtigste
- Cracken beschreibt die Konversion langkettiger Kohlenwasserstoffverbindungen zu kurzkettigen Molekülen wie Alkane, Alkene und Aromaten.
- Die Konversion kann auf verschiedene Arten durchgeführt werden:
- thermisch ohne Katalysator
- unter Zusatz von Wasserstoff
- mittels anderer Katalysatoren
- Beim thermischen Cracken sind Druck und Temperatur wichtig, um die Kohlenstoffverbindungen zu brechen.
- Beim katalytischen Cracken ist der Katalysator und das Reaktivieren dieses Katalysators von Bedeutung.
- Auch beim Reforming geht es um die Umwandlung von langkettigen Kohlenwasserstoffverbindungen. Hierbei wird jedoch die Struktur durch Isomerisierung, Cyclisierung oder Dehydrierung geändert.
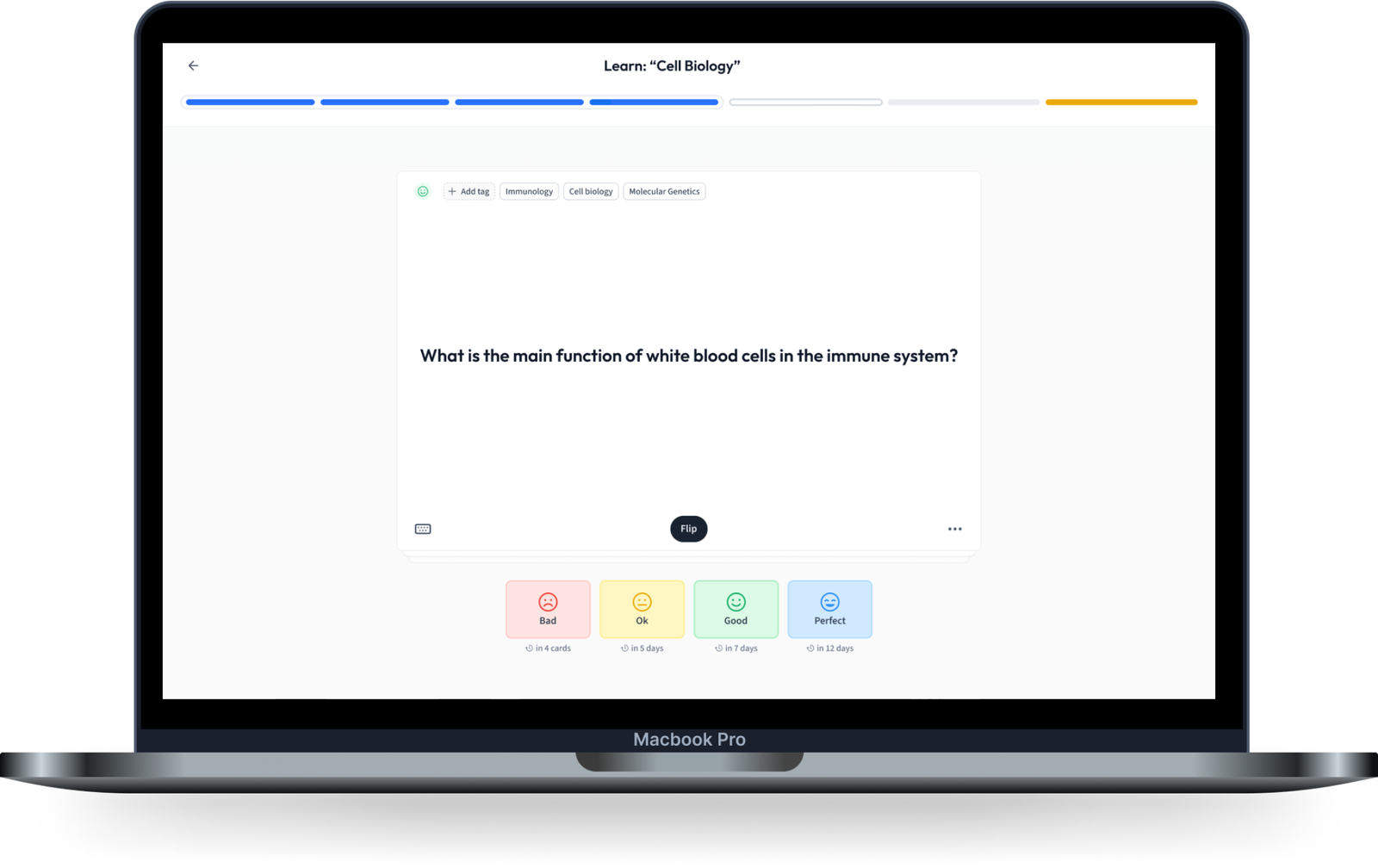
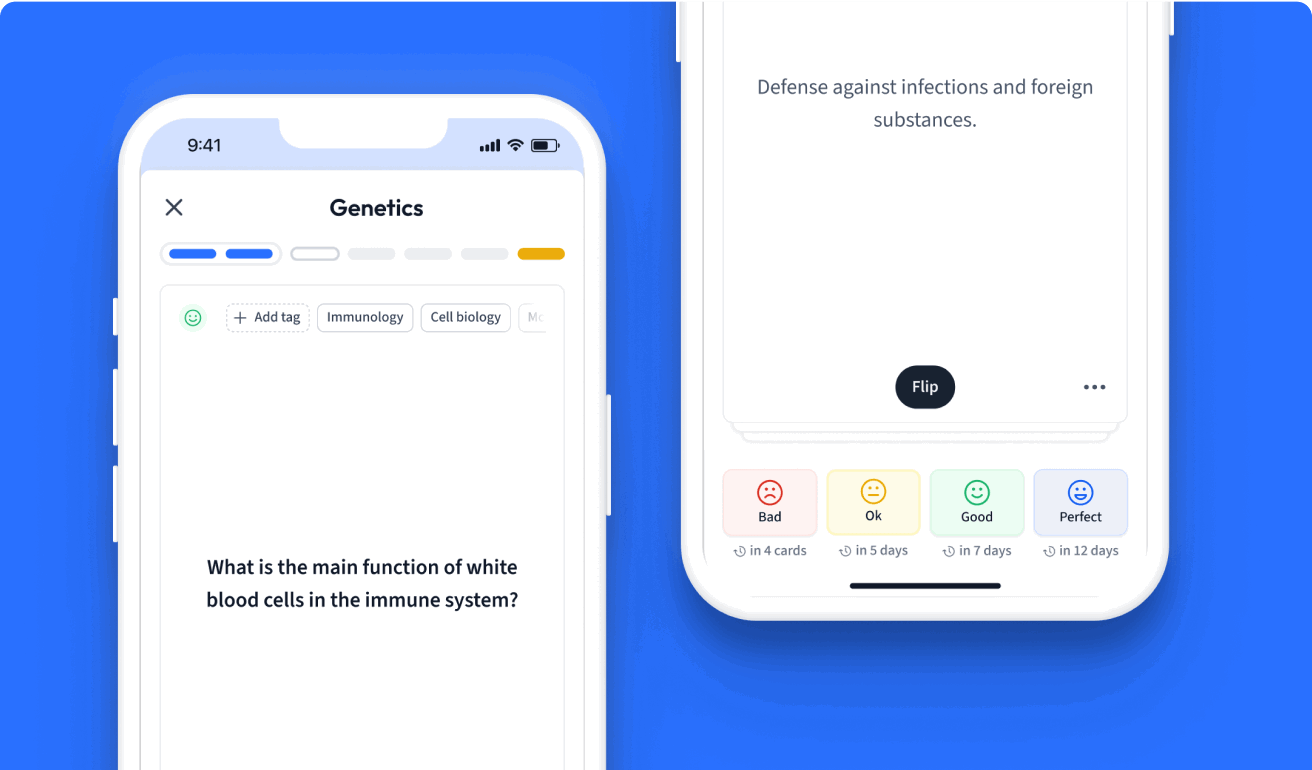
Lerne mit 15 Cracken Karteikarten in der kostenlosen StudySmarter App
Wir haben 14,000 Karteikarten über dynamische Landschaften.
Du hast bereits ein Konto? Anmelden
Häufig gestellte Fragen zum Thema Cracken
Was passiert beim Cracken?
Beim chemischen Cracken werden die Rückstände der fraktionierten Destillation des Rohöls in kurzkettige Kohlenwasserstoffe gespalten.
Warum wird Cracken angewendet?
Bei der fraktionierten Destillation entsteht eine große Menge an langkettigen Rückständen wie beispielsweise Schweröl. Die Nachfrage an Schweröl ist jedoch geringer als Benzin oder Dieselöl. Dabei handelt es sich um kurzkettige Kohlenwasserstoffe. Durch das Cracken sollen mehr und hochwertigere Dieselöle und Benzine gewonnen werden.
Wie funktioniert katalytisches Cracken?
Durch den Einsatz eines Katalysators wird die Spaltung der langkettigen Kohlenwasserstoffe erleichtert. Dazu wird das Vakuumdestillat der Rohöldestillation verdampft und anschließend mit einem Katalysator in einen Reaktor geführt. Dort findet der Crackprozess statt. Ziel ist es hochwertigere Benzine zu gewinnen.
Was passiert beim thermischen Cracken?
Beim thermischen Cracken werden die Kohlenwasserstofffraktionen in einem Druckbehälter auf Temperaturen von bis zu 800°C erhitzt. Durch Erhöhung von Druck und Temperatur entsteht eine Schwingung der langkettigen Kohlenwasserstoffe und die C-C-Bindungen brechen. Koks bildet ein unerwünschtes Nebenprodukt des thermischen Crackens.
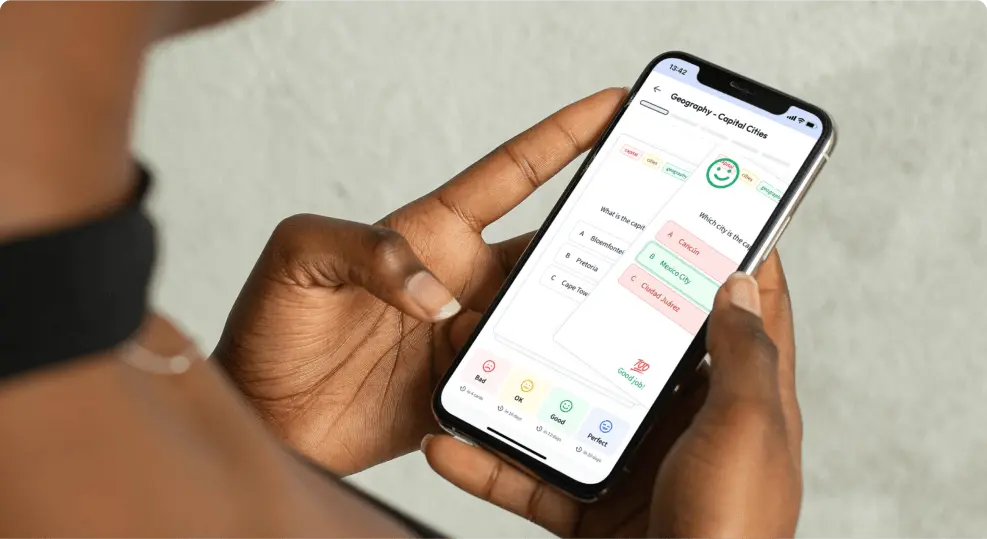
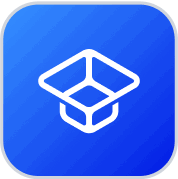
Über StudySmarter
StudySmarter ist ein weltweit anerkanntes Bildungstechnologie-Unternehmen, das eine ganzheitliche Lernplattform für Schüler und Studenten aller Altersstufen und Bildungsniveaus bietet. Unsere Plattform unterstützt das Lernen in einer breiten Palette von Fächern, einschließlich MINT, Sozialwissenschaften und Sprachen, und hilft den Schülern auch, weltweit verschiedene Tests und Prüfungen wie GCSE, A Level, SAT, ACT, Abitur und mehr erfolgreich zu meistern. Wir bieten eine umfangreiche Bibliothek von Lernmaterialien, einschließlich interaktiver Karteikarten, umfassender Lehrbuchlösungen und detaillierter Erklärungen. Die fortschrittliche Technologie und Werkzeuge, die wir zur Verfügung stellen, helfen Schülern, ihre eigenen Lernmaterialien zu erstellen. Die Inhalte von StudySmarter sind nicht nur von Experten geprüft, sondern werden auch regelmäßig aktualisiert, um Genauigkeit und Relevanz zu gewährleisten.
Erfahre mehr